Choosing the right injection moulding machine is a critical decision for businesses looking to optimize production efficiency and product quality. Injection moulding is a widely used manufacturing process that involves injecting molten material into a mould to produce precise and complex parts. In this article, we’ll explore how to select the most suitable injection moulding machine for your business needs, ensuring you make an informed and strategic choice.
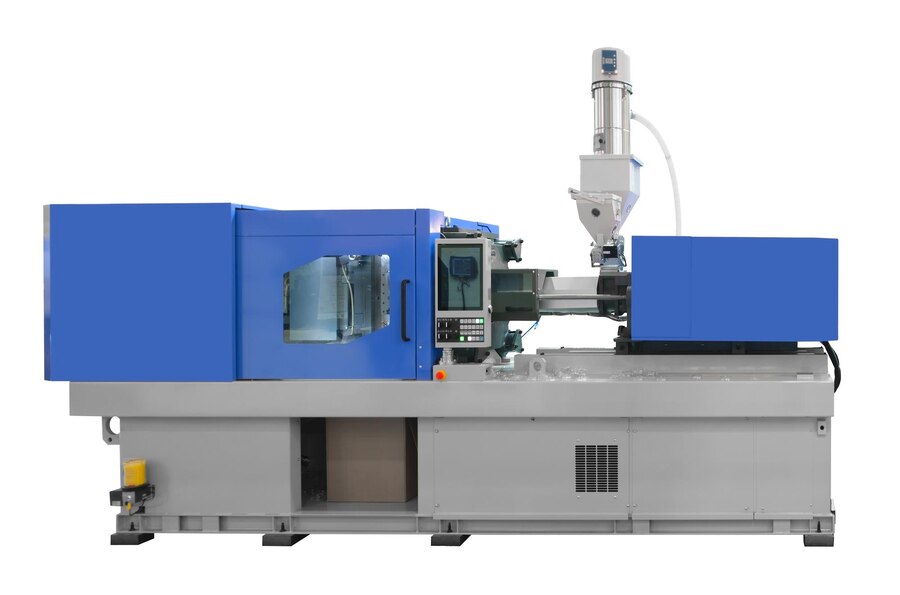
What is Injection Moulding?
Definition and Process
Injection moulding is a manufacturing process where molten material, typically plastic, is injected into a mould cavity. Once cooled, the material solidifies into the desired shape. This process allows for high precision and is ideal for producing large volumes of consistent parts.
Benefits of Injection Moulding
The primary benefits of injection moulding include high production efficiency, excellent dimensional accuracy, and the ability to produce complex shapes. Additionally, the process minimizes waste and can accommodate a wide range of materials.
Types of Injection Moulding Machines
Hydraulic Injection Moulding Machines
Hydraulic machines use hydraulic pressure to drive the injection process. They are known for their power and versatility, making them suitable for a broad range of applications. However, they are typically less energy-efficient compared to other types.
Electric Injection Moulding Machines
Electric machines operate using electric motors to control the injection process. They are highly precise and energy-efficient, with reduced operational costs. They are ideal for applications requiring high precision and lower production volumes.
Hybrid Injection Moulding Machines
Hybrid machines combine the benefits of hydraulic and electric machines. They offer energy efficiency while maintaining the power and flexibility of hydraulic systems. This makes them a good choice for applications that need both high performance and energy savings.
Key Factors to Consider
Production Volume and Capacity
The size and capacity of the injection moulding machine should match your production needs. High-volume production may require a larger machine with higher clamping force, while smaller operations might benefit from a compact model.
Material Compatibility
Different moulding machines are compatible with different types of materials. Ensure that the machine you choose can handle the specific materials required for your products.
Machine Size and Clamping Force
The machine’s size and clamping force must be sufficient for the mould and the parts you intend to produce. Insufficient clamping force can lead to defects and reduced product quality.
Energy Efficiency
Energy costs can significantly impact overall operational expenses. Consider machines with energy-efficient features to reduce long-term costs and environmental impact.
Cost and Budget
While it’s tempting to go for the cheapest option, it’s crucial to balance cost with quality and features. Investing in a machine that meets your requirements will save money in the long run by reducing maintenance and downtime.
Features to Look For
Automation and Control Systems
Modern injection moulding machines come with advanced automation and control systems. Look for machines with user-friendly interfaces and programmable features to streamline production and ensure consistent quality.
Maintenance and Support
Evaluate the manufacturer’s support and service offerings. Reliable maintenance and prompt support are crucial for minimizing downtime and keeping your machine running efficiently.
Technology Integration
Consider machines that integrate with other technologies, such as Industry 4.0 solutions, for enhanced data collection and process optimization.
Comparing Brands and Models
Leading Brands Overview
Some of the leading brands in the injection moulding machine market include Arburg, Engel, and Haitian. Research each brand’s reputation, product offerings, and customer reviews to make an informed choice.
Model Comparison
Compare different models based on their specifications, features, and performance. Look for models that best fit your production requirements and budget.
Case Studies and Expert Insights
Real-World Examples
Examining case studies of businesses that have successfully implemented injection moulding machines can provide valuable insights. For example, a company that switched to an electric machine might highlight significant improvements in energy efficiency and product quality.
Expert Opinions
Consulting with industry experts can offer tailored advice and recommendations based on your specific needs. Experts can provide guidance on the best practices for selecting and using injection moulding machines.
Future Trends and Developments
Technological Advancements
Stay informed about technological advancements in injection moulding, such as improvements in machine automation and material science. These developments can enhance production efficiency and product capabilities.
Market Trends
Monitor market trends to understand emerging demands and new technologies that could impact your decision-making process.
Practical Tips for Choosing the Right Machine
Evaluating Your Needs
Assess your production needs, including volume, material types, and desired product quality. This assessment will help you identify the most suitable machine for your operations.
Consulting with Professionals
Engage with industry professionals or consultants who can provide expert advice and help you navigate the complexities of choosing an injection moulding machine.
Conclusion
Summary of Key Points
Choosing the right injection moulding machine involves evaluating various factors, including machine type, production capacity, material compatibility, and cost. Understanding these aspects will help you make an informed decision that aligns with your business needs.
Final Recommendations
Investing in a high-quality injection moulding machine tailored to your specific requirements will improve production efficiency and product quality. Make sure to consider all relevant factors and consult with experts to ensure the best outcome for your business. read more…